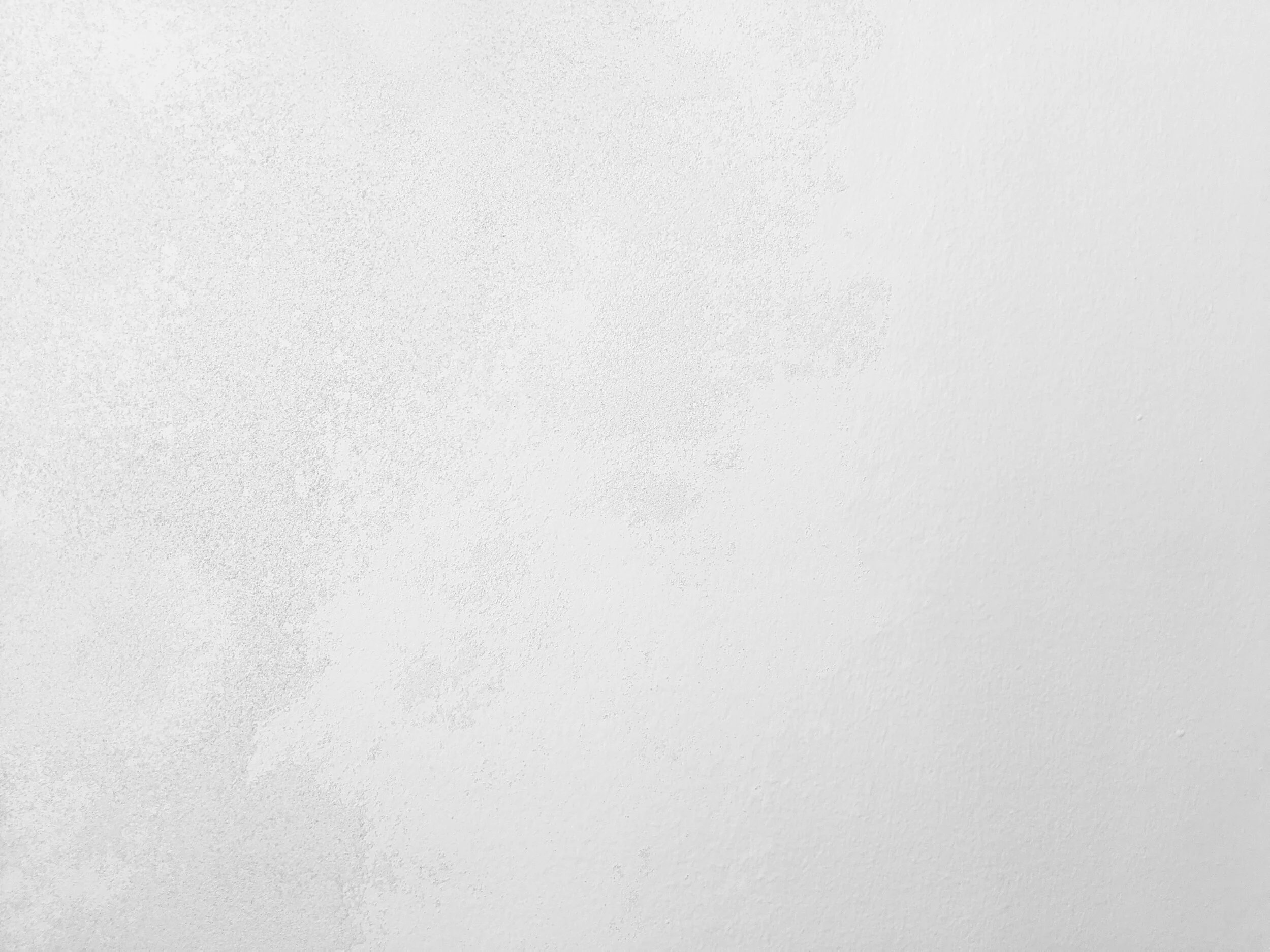
mani
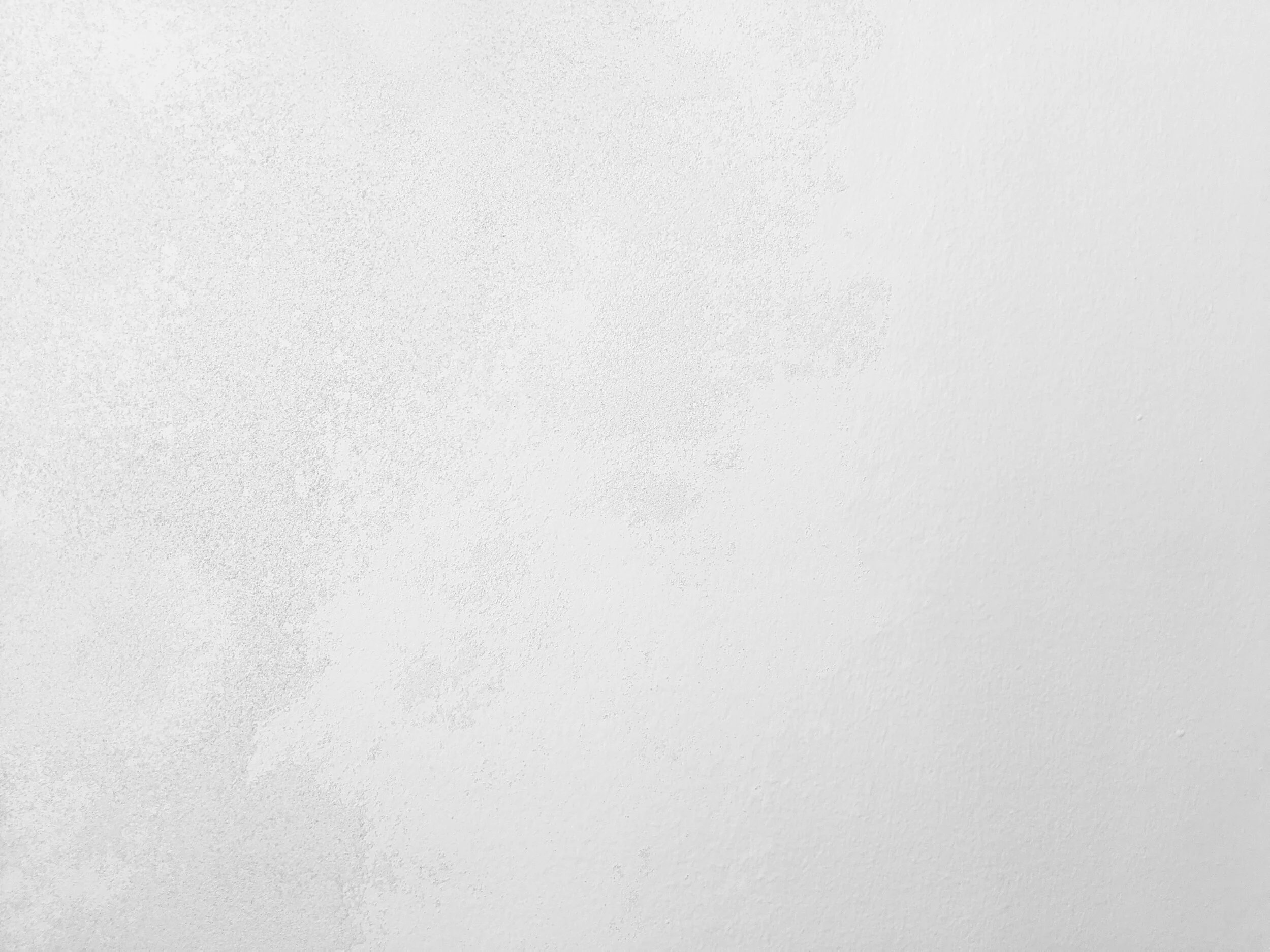
mani
Additive manufacturing as mass production is exponentially rising, but automation is needed to meet these high demands.
Within the seminar THINK.MAKE.START.ENTERPRISE. the BMW Group joined forces the Technical University of Munich to create a platform for intrapreneurship. Selected students and employees of the company would test new approaches and ideas for issues within the company by using the own the company’s channels and resources.
Additive manufacturing is gradually on the rise, it has even entered the field of mass production. The BMW Group uses their additive manufacturing department for custom and serial parts. Since the last year manufactured parts have risen by 42% and they are expecting to see an exponential increase in demand within the next year. 550 part are built everyday which are handled and supervised by only two overworked employees per shift.
In order to maximise the efficiency and profit, as well as reduce the stress on the workers, the team of SKAPE consisting of an robotics engineering, mechanical engineering student, me and two BMW employees has envisioned the MANI - the Manufacturing Assistive Navigating Intelligence unit.
It automates the process of refilling the additive manufacturing machines - 3D fusion printers by HP - with polymer trolleys, as well as removing empty trolleys from the printers. Further, the team developed a new printer schedule for optimised time management of the long running hours. The prototype for moving the trolleys was created from a ready automatic guided vehicle (AGV), provided by the BMW Group, and a custom created arm and hook. The latter was realised by CNC cutting aluminium parts and a linear motor which is initiated by a proximity sensor.
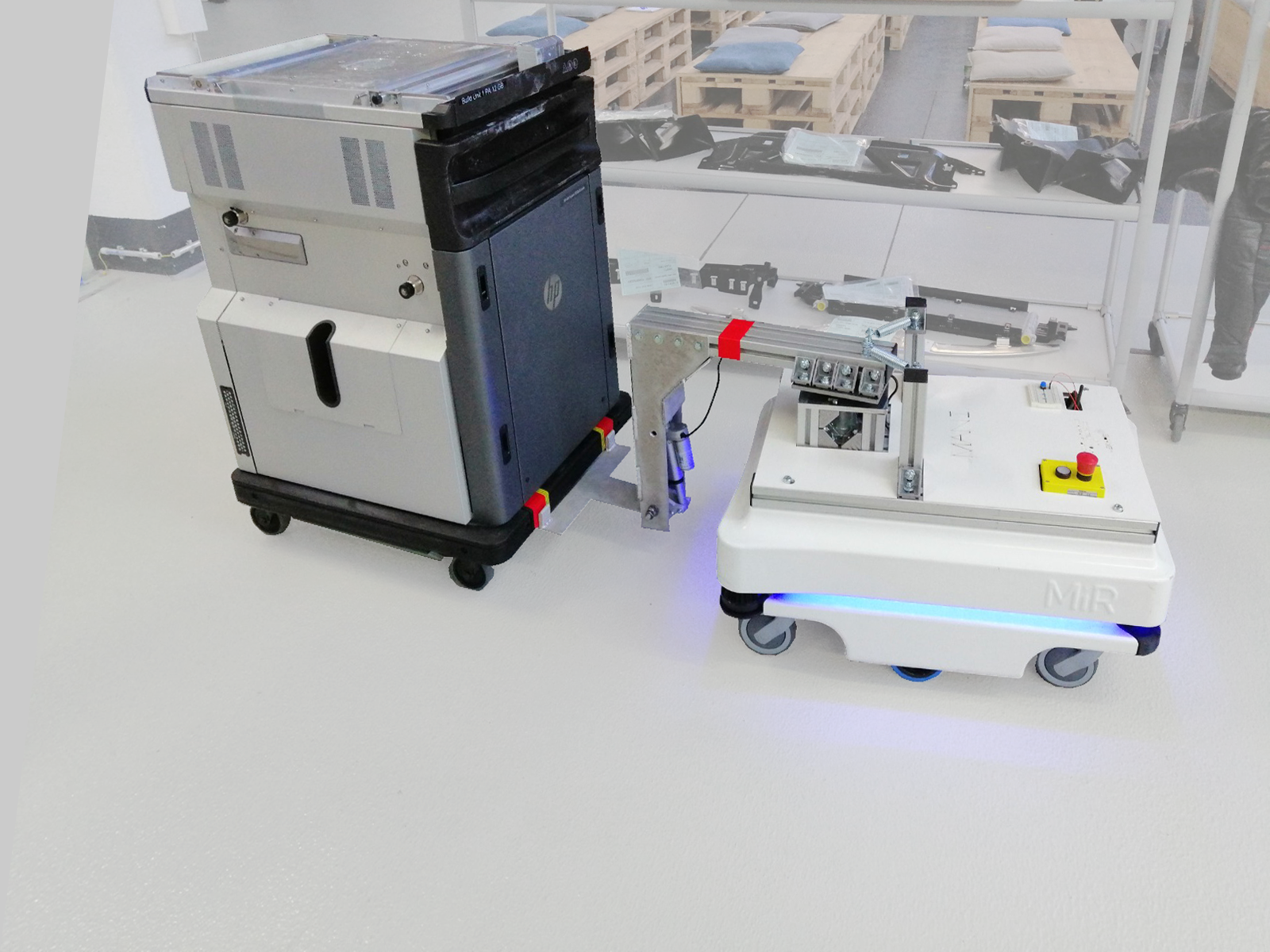
mani prototype
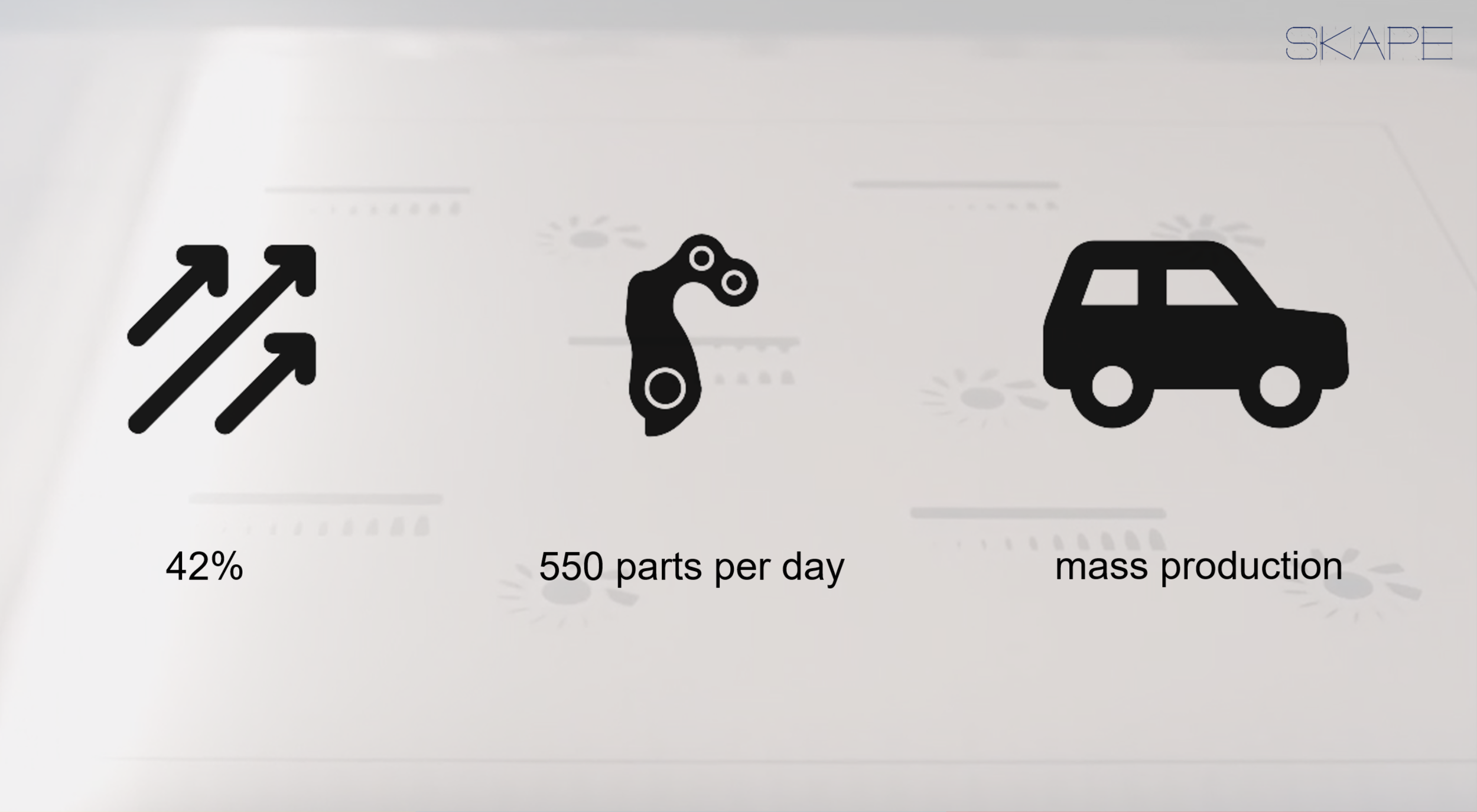
problem/ demands on additive manufacturing

solution/ automated material switch process

first drafts for necessary components

mani logo
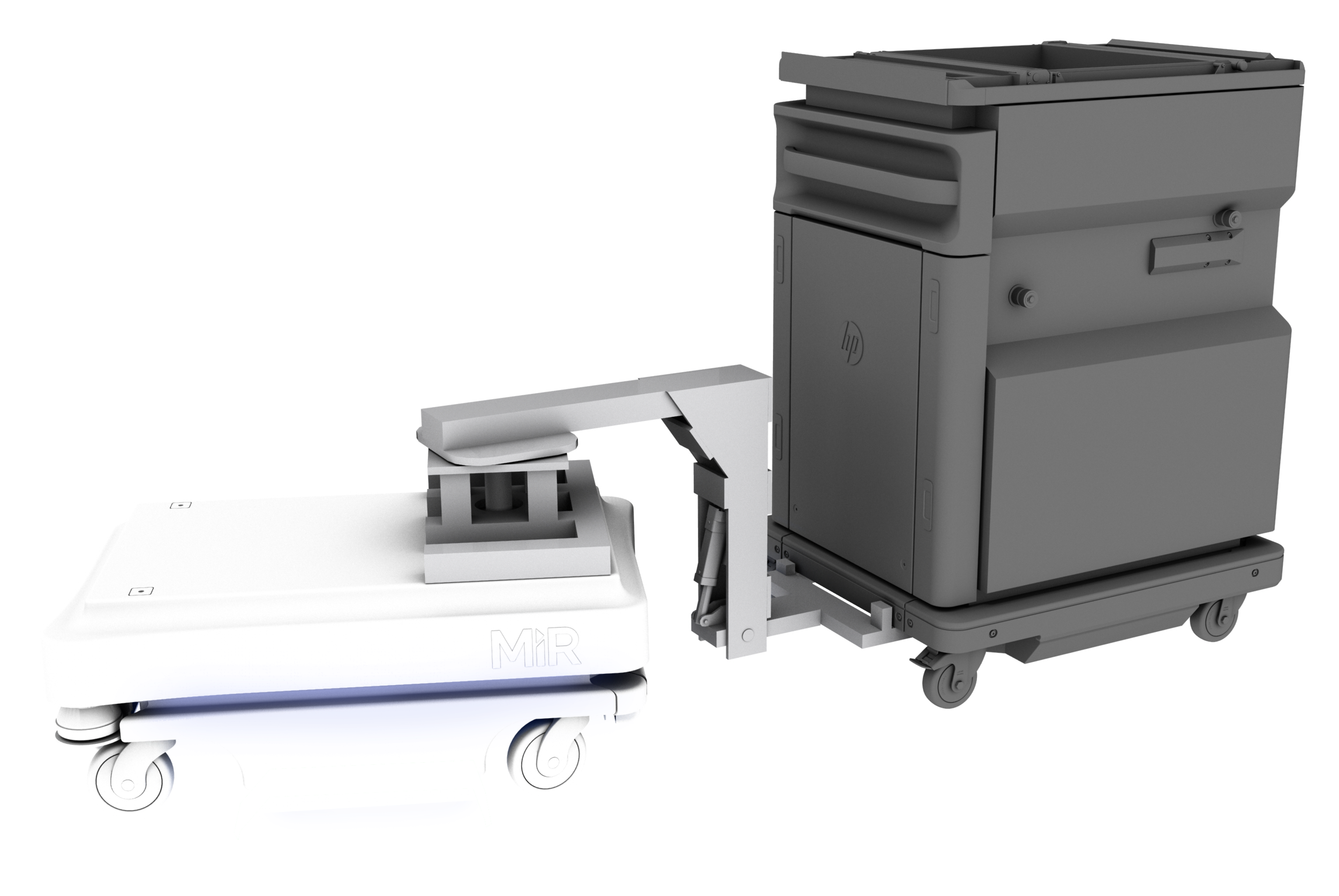
rendering/ AGV hooked to trolley
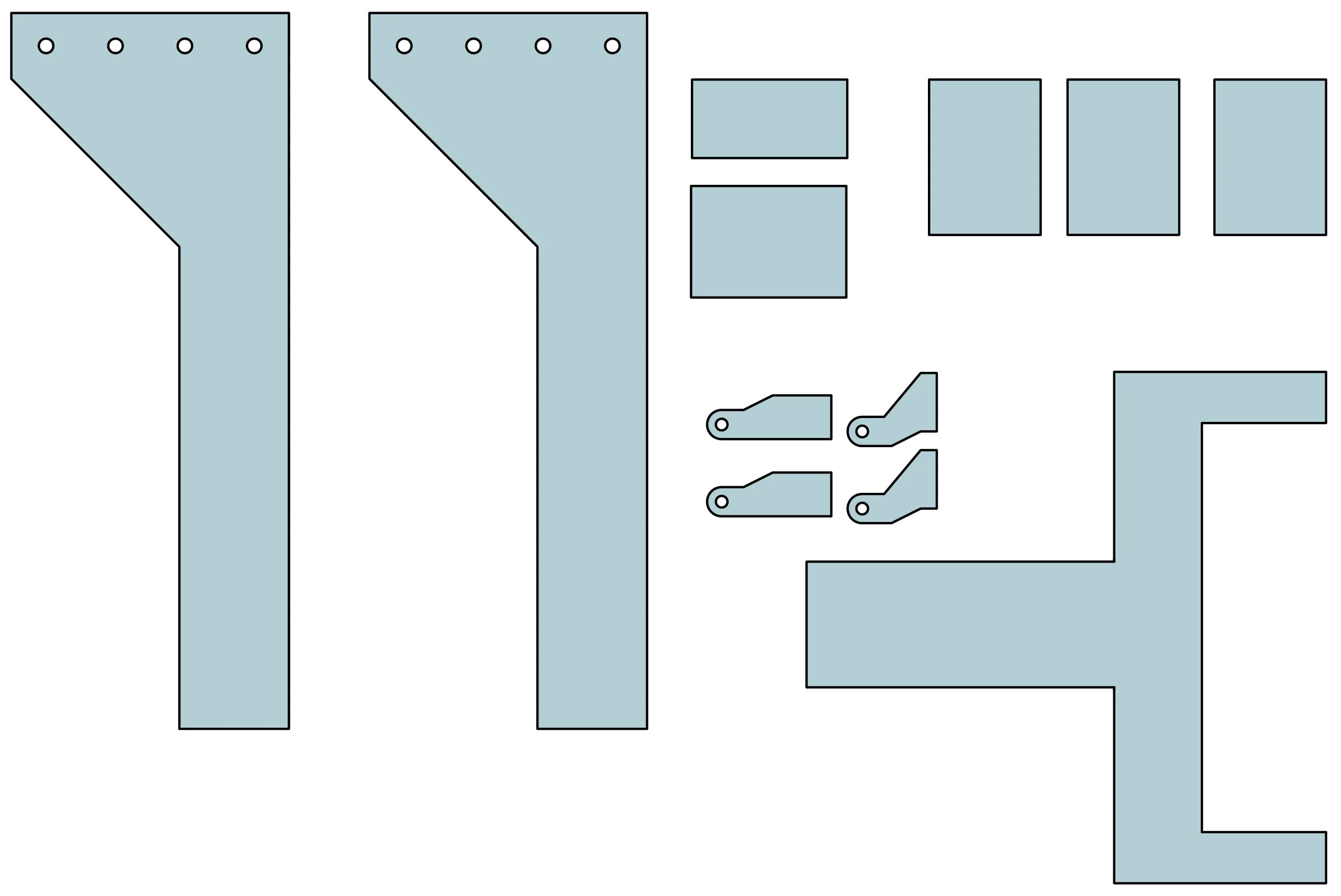
CNC-cut aluminium parts for custom arm and hook